An economic outlook for manufacturing: Jobs, technology, and resilience
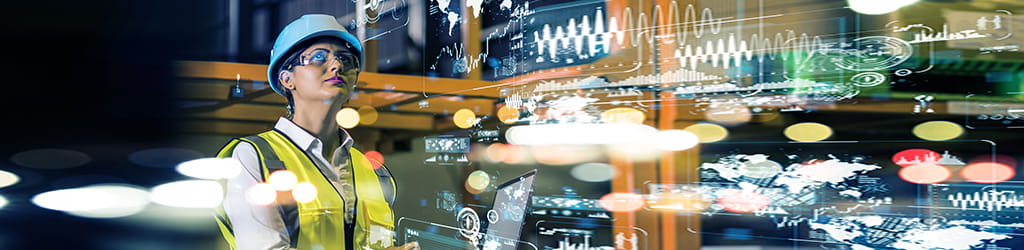
Chad Moutray is chief economist for the National Association of Manufacturers (NAM), as well as director of the Center for Manufacturing Research at The Manufacturing Institute, NAM’s workforce development and education partner. He recently shared with us a year-end Manufacturing Economic Update, covering the latest in industry and economic data and perspectives from NAM research. The information paints a picture of an industry that has shown “surprising resilience,” currently facing some challenges against the U.S. and global markets but also increased opportunities to innovate and grow. Read on for our top takeaways.
Economically, it’s a mixed view
There’s something of a “split-screen effect” happening across the industry, with sometimes contradictory positive and negative trends and perceptions. Manufacturing production numbers have stalled slightly, and several measures of manufacturer sentiment are low, including that over 63% of NAM survey respondents said they expect the U.S. to slip into a recession in 2022 or 2023. But demand remains high, as reported by manufacturers across the country. Although the manufacturing production number only edged up about 0.1%, that was still the best number seen since July of 2008. And as we will explore in the next two sections, employment is strong, and companies are investing in themselves to be able to meet the demand that’s out there. In the October survey, 75% of NAM respondents were positive about their company’s outlook – a historic average, despite being down from other months this year.
- On the global level, there are three main “buckets” of challenges:
- China’s “zero COVID” policy leading to factory closures, restrictions on consumer spending, and overall sluggish growth, which can expand to the rest of Asia
- Slowing global trade in general, as many countries struggle to meet debt obligations against a strong dollar
- Europe being in or going into a recession, with high inflation especially for food and energy costs, due in part to sanctions on Russian oil
- In the U.S., the strong dollar has a nuanced impact for manufacturers – it’s detrimental to exports, but benefits imports. High energy costs will likely be a challenge here, too, as the industrial sector consumes 30% of all energy produced in the U.S.
Expand the workforce by opening doors and minds
The big, bright spot in today’s economy is the job market. The U.S. added more jobs last year than ever in the history of data-keeping. It was admittedly what economists call a “dead cat bounce” – a burst of recovery within an overall decline – but still, the job market looks strong. In September, the unemployment rate was 3.5% – the same as it was in February 2020, which was the lowest since December 1969. In October, it was up slightly to 3.7%, but in this economy, that could be considered full employment. The number may start creeping higher as we move into 2023, especially if we were to go into a recession – maybe to over 4%, 4.5%, even 5%. But compare that to the Great Recession: Unemployment then peaked at 10%. This is a unique moment in time.
In highlighting low unemployment, it is worth noting that the U.S. labor force participation rate is nowhere near where it was before the pandemic – more than a full percentage point below – due to factors such as:
- The pandemic sparked a lot of accelerated retirements.
- People are choosing work-life balance differently.
- Childcare is a major problem in manufacturing, with childcare deserts around the country.
- Immigration policies are tighter than in past years.
Labor force participation levels likely will not get back to pre-pandemic levels, partially due to demographics, as more older workers retire. And economists also estimate that we’ve lost about 3.5 million workers compared with where we would have been if not for the pandemic, including the million-plus Americans lost to COVID-19, about a quarter of whom were working-age.
Still, the manufacturing industry added 367,000 workers this year, through the first 10 months of 2022, surpassing last year’s 365,000, which had been the most since 1994. It’s another dead cat bounce – the industry lost 1.3 million workers in the first two months of the pandemic – but still, the overall worker count is now at a level of employment not seen since 2008: 12.92 million Americans in manufacturing.
The challenge is: Over the past year, the industry has averaged 850,000 job openings. Nationally, there are about 10.7 million job openings in all sectors, and about 5.7 million unemployed Americans. So, for every 100 job openings – not just manufacturing, but for everybody – there are only 54 unemployed Americans looking for jobs.
With everyone looking for workers, wages are on the rise, and manufacturers are struggling to find entry-level workers as they are competing with not only industry peers, but also fast food, major retailers, and other places that hadn’t previously been a challenge. NAM members have reported having to raise wages several times over the last couple of years to stay competitive. The industry is still paying more than most, but the gap has narrowed, and again, people are looking at work-life balance differently.
One potential major solution to this shortage is going to be increasing the pool of workers in manufacturing.
- NAM is working to encourage more women to participate in manufacturing. Right now, women make up 29% of the manufacturing workforce; the goal is to increase that to 35% by 2030. That’s about 800,000 women – almost enough to fill that average number of job openings.
- NAM is also supporting programs around the country to encourage military veterans leaving service to go into manufacturing, bringing their strong skill sets.
- Second chance hiring is on the rise: programs that encourage companies to consider candidates with previous convictions that might otherwise hurt their ability to get hired.
- The Manufacturing Institute now manages the FAME – Federation for Advanced Manufacturing Education – apprenticeship program, first launched by Toyota, which provides “workforce development through strong technical training, integration of manufacturing core competencies, intensive professional practices, and intentional hands-on experience to build the future of the modern manufacturing industry.”
The other major mission will be just working to change perceptions about manufacturing. It’s not dark, dirty, and dangerous; it’s a highly sophisticated, well-paying industry. Which is a good segue to…
Manufacturing is a tech field
Consider for a minute the changes currently underway in the auto sector. The move from gas combustion vehicles to electric vehicles and hybrids essentially changes the whole makeup of a car – you’re essentially driving a smartphone. So while the type of worker needed in production is still similar, the underpinnings are all different, and auto companies are competing for technology engineers more and more with Silicon Valley.
That’s the clearest example of the shift happening across manufacturing as the industry becomes more technologically advanced. Last year, manufacturers bought more robots than in any previous year. Companies are investing in automation, AI, data visualization, 3D printing, and connected technologies in ways that they weren’t before. Supply chain challenges, and increased moves toward reshoring and nearshoring as freight costs rise, are requiring companies to be smarter about procurement, which is pushing progress in data and digitization. All of these advances can save costs in addition to making a company more competitive.
These investments are blurring the lines about what is a manufacturer and what is not – and that, in turn, requires hiring a different type of worker, along with more upskilling of existing teams. There may be an opportunity for manufacturers to draw in workers amid the spike in tech sector layoffs, though it may be a challenge to recruit tech workers to work in areas other than Silicon Valley. But again, the lines are blurring. Microsoft, after all, is a member of NAM. Many major manufacturers make as much money, if not more, from services as factory.
In some ways, these trends in jobs and technology can help solve each other. Technological advances can help attract workers to the industry, and can also drive efficiencies that help close the labor gap, such as automating jobs that are harder to recruit for.
But a very important thing to note is that companies aren’t letting people go as they increase automation; they’re upskilling, and moving people around the factory to do other tasks. Robots aren’t taking jobs; they’re complementing labor, and allowing companies to be most efficient with the people they have. While that might not always be the case, it is for now.
In conclusion
All in all, Moutray’s forecast for the manufacturing industry is positive: Likely a short recession and sluggish growth in the first part of the year, but coming out of it toward the year’s end. As long as people are still working, seeing wage growth, and able to spend, he projects a possibility for a “soft landing,” and continuation of the resilience we’ve seen so far.
Contact
Let’s start a conversation about your company’s strategic goals and vision for the future.
Please fill all required fields*
Please verify your information and check to see if all require fields have been filled in.
Related services
This has been prepared for information purposes and general guidance only and does not constitute legal or professional advice. You should not act upon the information contained in this publication without obtaining specific professional advice. No representation or warranty (express or implied) is made as to the accuracy or completeness of the information contained in this publication, and CohnReznick, its partners, employees and agents accept no liability, and disclaim all responsibility, for the consequences of you or anyone else acting, or refraining to act, in reliance on the information contained in this publication or for any decision based on it.