6 keys to robust, effective inventory planning and management
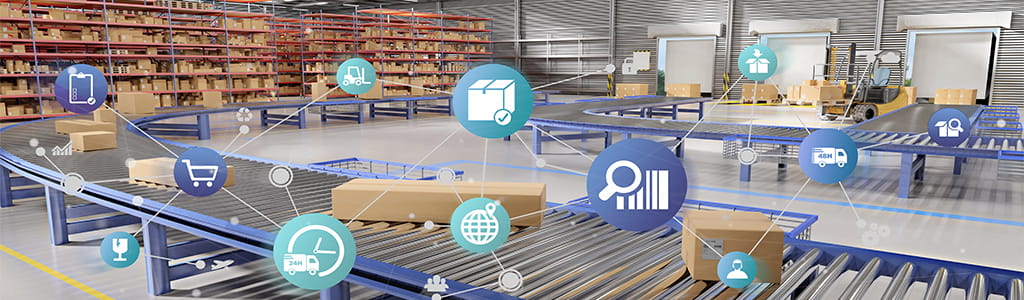
Inventory accounting and reporting can be complex. Cost is incurred at all stages leading to the eventual sale of goods; accounting for it properly includes all activities, such as procurement-related activities, receipt of goods in the warehouse or at the third-party logistic provider (3PL), manufacturing (i.e., converting raw materials into finished goods), and storing the finished goods before shipping them to the end customer. But it’s a critical process to get right: Whether your company uses a “Standard” or “Direct” costing system, robust cost accounting allows for better business decisions and a thorough understanding of the margin and profit drivers.
Consider these six key areas as you build out a robust inventory and supply chain production and management.
- Review and develop processes for cycle counts and physical inventory counts. Reviewing the count and process, you validate the existence assertion and support lender/bank reporting requirements.
Full physical inventory counts require significant time and resources, but they are essential to keeping inventory records accurate and current. These involve counting and verifying all physical items in stock, and confirming inventory records’ accuracy and completeness. Depending on the inventory quantity and the stock locations, this process can take several hours to several days. Allocating a team of employees dedicated only to conducting the inventory count is critical to an efficient and accurate process. The cost of pausing business operations during the inventory count should also be considered. This process is essential to maintaining accurate inventory records and supporting effective decision-making.
Cycle counting is an effective process that validates the accuracy of the inventory quantities in the company’s enterprise resource planning (ERP) or warehouse management system. It is a more efficient inventory management approach than full physical inventory counts. Cycle counting provides a regular and systematic process of a predetermined set of inventory items, instead of counting all inventory. This approach helps minimize disruptions to daily operations, allowing businesses to maintain regular workflow with minimal interruptions. Cycle counting also enables organizations to continuously identify and correct inventory inaccuracies; a cadence of cycle counting can immediately identify and correct any discrepancies. All of this can help organizations improve the efficiency and accuracy of their stock.
- Develop or review the standard costing practices from ASC 330 and IAS 2 for capturing appropriate direct and indirect costs. All costs incurred are not capitalizable under ASC 330 and IAS 2 guidelines. Understanding costs that qualify for capitalization and quantification is key to:
- Accurate financial reporting – matching expenses with revenues
- Timely and relevant information for decision-making
- Evaluating performance over multiple periods
Several factors require consideration when evaluating the cost of products and services:
- First, the cost of raw materials or inputs needed to produce the product or provide the service is identified. This includes materials, the cost of procuring the raw materials, direct and indirect labor, and other expenses directly associated with production.
- Next, any fixed direct or indirect costs necessary for running distribution or manufacturing operations are added, such as rent, depreciation, utilities, and insurance.
- Variable costs, which fluctuate with activity levels, are also included. Freight and transportation expenses are one example.
The above standard cost approach provides businesses with a thorough understanding of what they need to cover for overhead costs and include them in the pricing and margin calculations. Ultimately, this will help businesses evaluate generating a competitive profit margin.
- Prepare inventory account analysis with supporting schedules for audit or transaction readiness. An inventory rollback and roll forward approach provides a snapshot of inventory as of the rollback or roll forward cutoff date, allowing the company to validate its period-end perpetual inventory and general ledger activity. As part of the audit readiness process, auditors and the company management will often perform a full inventory count and perform a reconciliation of these inventory counts to the general ledger. Organizations should develop a template that gathers all the information needed for a rollback or roll forward based on the last physical inventory count and reconcile to financial records.
- Build best-practice policies, procedures, and controls for the inventory process lifecycle. This includes:
- Receiving: Distribution managers understand that outbound success and efficiency depend on the success of inbound efficiency and performance. Best practices include supplier packaging, carton labeling, and enforcement of vendor compliance manuals.
- Slotting: Slotting assigns specific locations or slots for storing inventory items. It involves determining an optimal location for each item based on various factors, such as size, weight, demand, and accessibility. By effectively slotting items within a warehouse, companies can improve efficiency, reduce picking times, and maximize storage space.
- Putaway: Putaway is the process that moves material from the receiving area to the storage, replenishment, or pick areas or into the manufacturing operation. Companies should use cross-docking when possible to move specific products to support an open order or replenishment request. (Cross-docking is the practice of unloading and loading delivery vehicles in the same cartons as they were received without having to put away merchandise.)
- Develop a dashboard of key performance indicators (KPIs). The development of timely and reliable management reporting helps organizations understand their inventory and how to measure its success and overall performance. Moreover, KPIs allow companies to benchmark themselves against their past performance and their peers. However, measuring against inaccurate information impacts proper inventory planning. Organizations should consider developing a warehouse metrics dashboard with KPIs such as:
- Order fill rates – Sales
- Stock-to-sales ratio – Sales
- Inventory turn – Sales
- Lost sales ratio – Operational
- Order cycle time – Operational
- Shrinkage – Operational
- Be prepared for inventory cost due diligence. In the event of a sale, potential buyers want to understand the following during their due diligence review of a company:
- Valuation process: What methodology does the company use, and which costs are capitalized to the balance sheet (e.g., purchases, labor, overhead allocations)? How often are the standards analyzed for appropriateness if standard costing is used? If the inventory is not properly valued, the buyer will want to adjust the net working capital, as the value received at close does not equal the reported amounts.
- Physical count: What procedures are in place for the physical counts, and how often are counts performed? What discrepancies are typically identified during the counts, and are they resolved timely? Can the buyer trust the number of units recorded in inventory to calculate its value?
- Turns and aged inventory: Are inventory turns increasing over time, leading to potential aging inventory that cannot be sold? A buyer may request to exclude any aged inventory that cannot or is unlikely to be sold from the transaction.
- Reserve methodology and historical write-offs: If the reserve is inadequate, the buyer will request an adjustment to net working capital to reflect a more proper inventory valuation.
- Changes to inventory levels: Can the management team effectively manage inventory levels, even with supply chain challenges, and not tie up the company’s cash flow?
Having good inventory management practices and management helps companies make sound strategic decisions in preparing for growth. Building sustainable inventory processes and methods to measure progress will help determine necessary business adjustments. CohnReznick can help provide the foundation and identify ways for developing best practices tailored for your organization.
Contact our team to learn about our inventory costing services to get started on optimizing your cost accounting.
Contact
Eric Wade, Managing Director, CFO Advisory
704.900.2504
Derek Delisle, Senior Manager, CFO Advisory
617.648.1409
Contact
Let’s start a conversation about your company’s strategic goals and vision for the future.
Please fill all required fields*
Please verify your information and check to see if all require fields have been filled in.
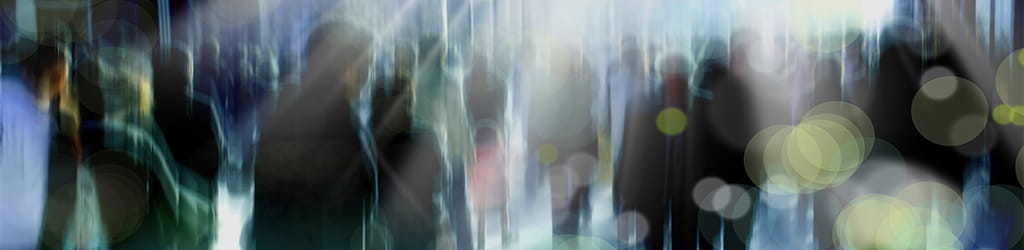
Building the Organization of the Future
This has been prepared for information purposes and general guidance only and does not constitute legal or professional advice. You should not act upon the information contained in this publication without obtaining specific professional advice. No representation or warranty (express or implied) is made as to the accuracy or completeness of the information contained in this publication, and CohnReznick, its partners, employees and agents accept no liability, and disclaim all responsibility, for the consequences of you or anyone else acting, or refraining to act, in reliance on the information contained in this publication or for any decision based on it.